Mineral refining
Mineral refining is essential for transforming raw materials into materials needed for battery production, with lithium being particularly important due to its high energy density. As demand for lithium-ion batteries rises, efficient and sustainable mining and refining processes are crucial in. Innovations like direct lithium extraction and improved brine processing, are key to meeting the demand of battery-grade chemicals while minimizing environmental impact.
Alfa Laval helps you achieve:
- Boosted product recovery
- Optimized product purity
- Improved energy efficiency
- Sustainable water management
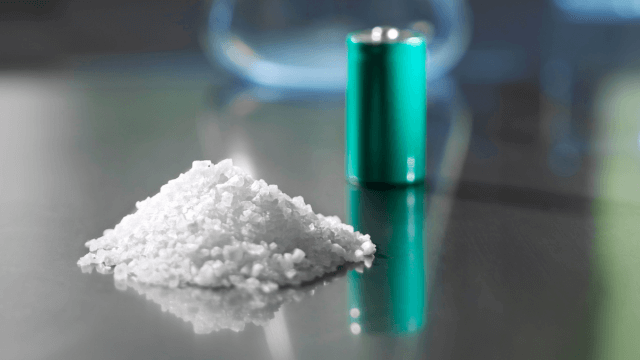
Process overview
In lithium refining, the feedstock is from either brine or hard rock. Brine extraction involves evaporating water from lithium-rich brine, leaving a concentrated solution, while hard rock mining processes spodumene ore through crushing, heating, and leaching. The resulting lithium sulfate or concentrated solution is then refined to produce lithium carbonate or lithium hydroxide. The lithium carbonate or lithium hydroxide are then sent for further processing at a gigafactory ahead of being integrated into a battery’s cathode material.
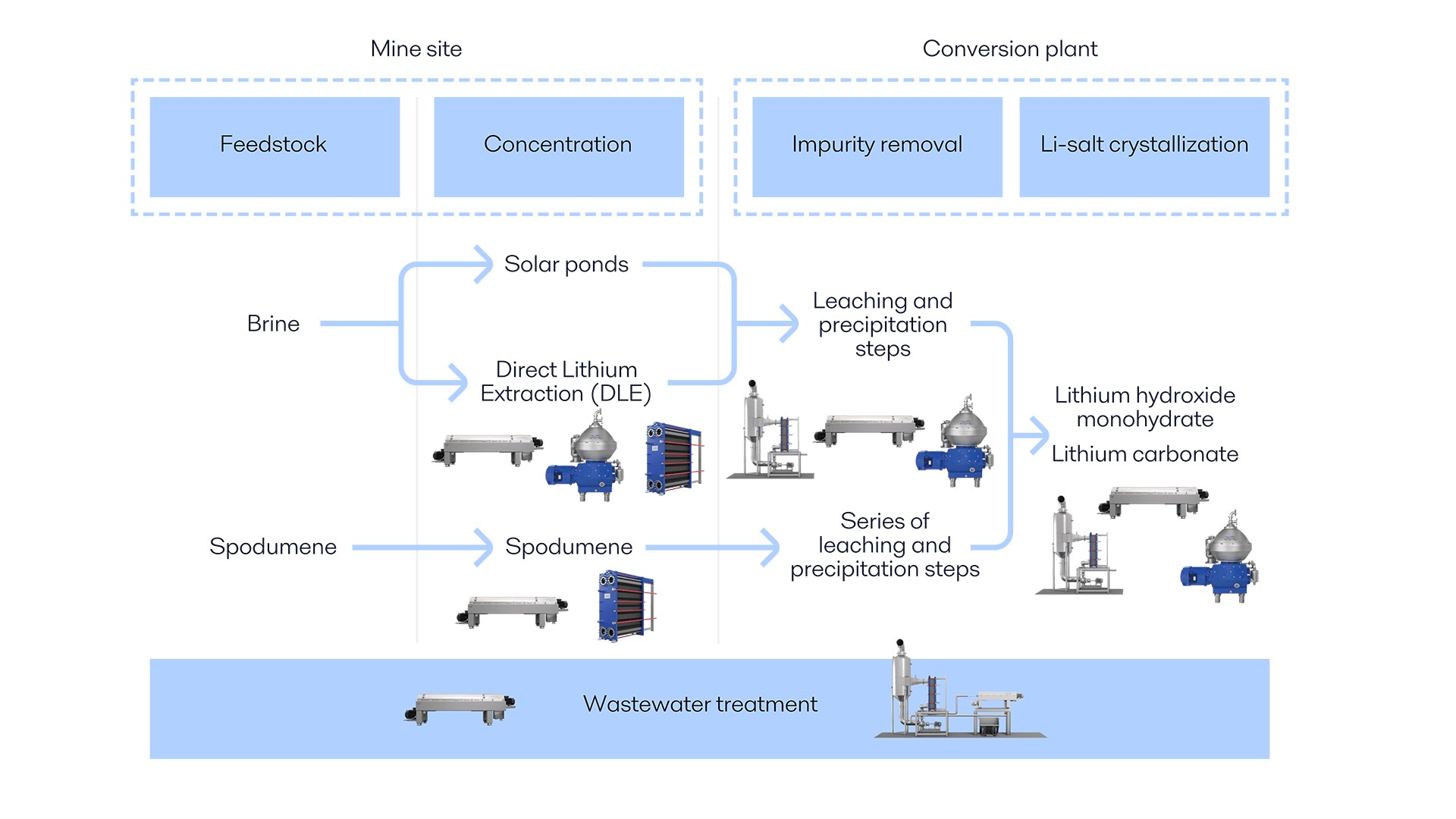
Meeting mineral refining needs with cutting-edge solutions
Alfa Laval’s separation and heat transfer solutions provide process improvements within different mineral refining processes. Within lithium refining, evaporation systems fit perfectly where the lithium product and by-products need to be crystalized, while centrifugal separation solutions can be used for separating the impurities or crystals of products from the liquid solution.
Furthermore, as refining processes produce large amounts of wastewater, an energy efficient wastewater treatment is needed to reduce costs and the impact on the environment. With Alfa Laval ZLD technology, the waste decreases in both weight and volume, while the water can often be reused. Often, valuable materials can even be recovered for reuse, which would have been lost otherwise.
Evaporation
Alfa Laval’s evaporators are highly efficient thermal systems that have been optimized to concentrate process liquids economically, while also preserving the quality of the final product. This is usually the case for recycling streams where the concentration of the desired compounds are very low.
As lithium mining produces a large amount of wastewater, evaporation is a key part of the treatment process. This process makes it possible to separate the waste materials and recover water and other materials for reuse.
Decanter centrifuges
Decanter centrifuges provide efficient in solid-liquid separation, important for the removal of impurities in mineral refining processes and separating the recovering the final product.
Decanter centrifuges also play a key role in the treatment of the wastewater, supporting the recovery and reuse of water and other key materials.
Disc-stack separators
Disc-stack separators are reliable and highly efficient separators that can be used both for solid-liquid separation, as a polishing step after the main separation step, or liquid-liquid separation which is needed for successful implementation of solvent extraction.
Compared to other separation technologies, Alfa Laval disc-stack often operates at a lower cost, lasting longer, and reducing downtime.
Zero liquid discharge
Alfa Laval Zero Liquid Discharge (ZLD) systems are robust, compact solutions that are used both in the main process as crystallizers and in the wastewater stream to minimize the liquid discharge.
Heat transfer
Alfa Laval offers a wide range of gasketed and welded plate type heat exchangers that are highly efficient, compact, and flexible in their design. These exchangers are utilized throughout both hard rock and brine lithium extraction methods.